Resources
Our latest thoughts on labeling and artwork management
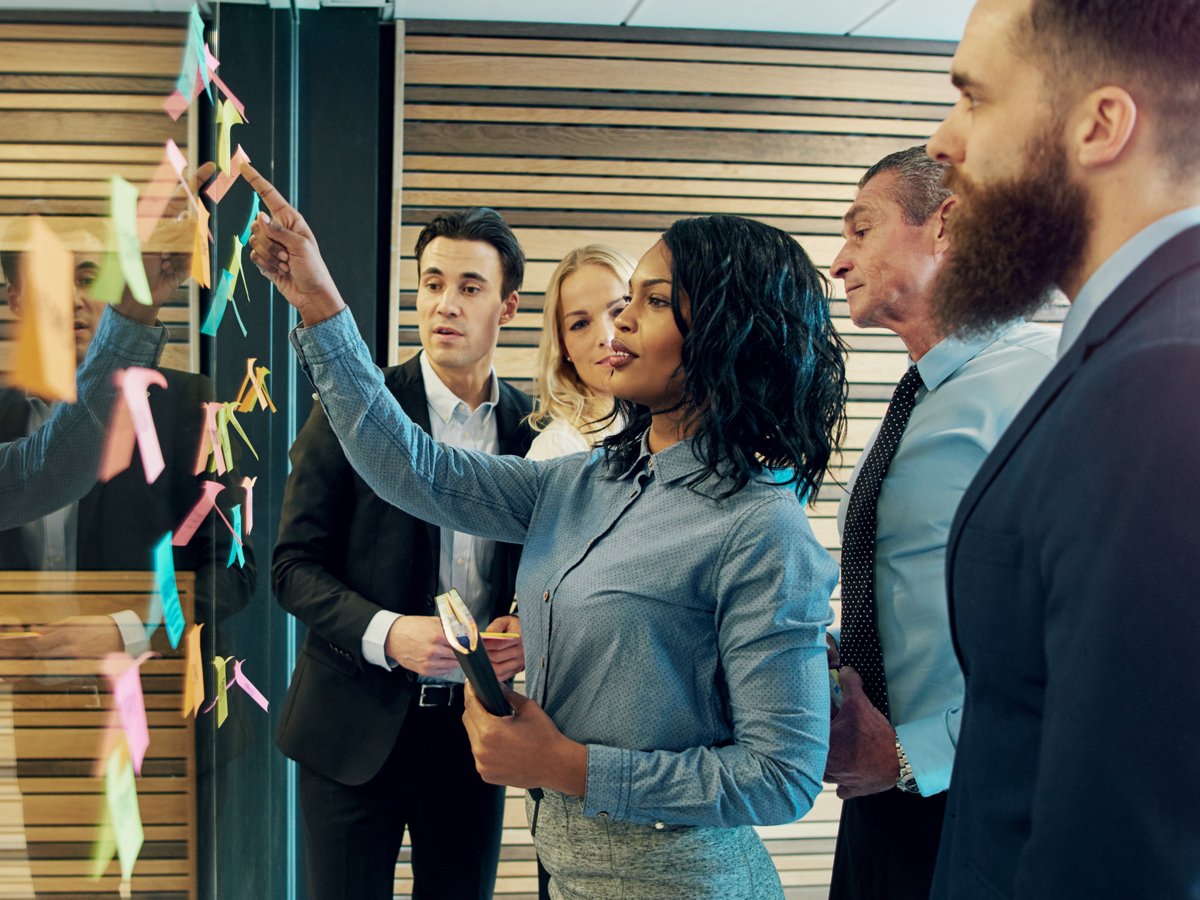
See featured resources
Other
Labeling Maturity Assessment
Are outdated labeling processes holding you back? Complete this 10 question survey to get your personalized assessment,...
White Paper
Fashion's sustainable evolution: Navigating regulatory compliance with the Cloud
Download this whitepaper to learn how cloud-based labeling helps fashion retailers to ensure supply chain traceability,...
White Paper
The role of AI and automation in the food and beverage industry
Download this whitepaper to learn how automation through cloud-based labeling helps food and beverage companies to...
White Paper
Injecting agile production methodologies into clinical trials
Read this report to see how the industry has shifted its approach to how clinical trial supplies are managed and as a...